Air Cylinder Allows Ultra-Fine Tension Control
An air cylinder provides smooth operation and controls tension to less than 0.5 gram to produce special fiber sensors that are as small as 0.0013-in. diameter
Applying tension is a very common requirement in a variety of manufacturing operations. But sometimes high precision is needed in the control of the tension. For those situations, a nearly frictionless air cylinder can actually eliminate a traditional spring-loaded tensioner and provide a level of control not possible with ordinary air cylinders. In the spooling operation at a major fiber technology company this has been done with repeatable control over the tension in a closed loop system to less than 0.5 grams, with a response time constant of less the 0.1 second.
Winding operations are one example where tension is used to control how a material is wound onto a reel. If the material is large copper cables, the tension requirements may not be that severe. But for very small diameter or fragile materials, controlling the tension is critical. Otherwise the material can stretch, break, or be wound with uneven tension. An example is the manufacture of nano-technology fiber sensors. These sensors consist of long strands of material with special coatings, used in medical and other high specification applications. One of these fiber sensors, for example, consists of a 0.0013 in. diameter silver wire that is coated with a proprietary elastomer. This sensor is threaded into the human blood stream where it can monitor blood pressure, acidity, oxygenation, temperature and carbon dioxide. It is amazing technology, but very difficult to manufacture. The manufacturing system involves the spinning and drawing of fiber sensors. Fiber emerging from an extruder is first drawn down by traction. A laser measures the fiber diameter and is used in a feed-back loop to control the tension. A heater is often used to align the molecular structure of the polymers to increase tensile strength and flexibility. Tension is measured after this heating process and just prior to achieving the final desired fiber diameter. Feedback from the tension measurement apparatus and another laser are again used to control tension. Finally, the finished fiber is wound onto a series of spools, whose tension is controlled independently to customer specification. This is done to match the end user’s equipment requirements for the tension consistency and payout velocity. In most applications such as this, tension is achieved by applying force with a spring wound dancer. This consists of a wheel attached to a spring, which moves up and down in response to changes in force. Variations in line speed, wheel size or fiber size all drive changes in the tension on the fiber. The goal is to provide a constant tension on the line. The dancer arm effectively dampens variation in force to even the applied tension. Changing the overall level of tension, however, usually requires a hand adjustment of the spring loading.
For the manufacture of these types of fibers much more precise control of the manufacturing process is required. In particular, the fiber tension needs be adjustable from 5 to 150 grams with an accuracy and repeatability of 0.5 gram. To obtain this precision, and to increase the versatility of the fabrication line, engineers decided they needed a computer controlled, closed loop system to automate adjustments in tension. First, the shaft of the dancer arm was augmented with an optical encoder to provide highly accurate positional data. Using internally developed algorithms, the position of the shaft was first used to control the driving motor speeds in a closed loop system.
But problems were immediately apparent; the control system was unstable. The dancer arm oscillated back and forth, while the computer struggled to adjust the tension. For the most part, this was caused by the low inertial mass of the fibers, whose tension the dancer arm was trying to control. The result was uneven tension application, fiber stretching and worse fiber breakage. The solution was to replace the spring with an air cylinder. An ordinary air cylinder would not do because most use elastomeric (rubberlike) seals that produce jerky and erratic motion. These devices cannot achieve the precise and repeatable force needed for this application. The cause of the erratic motion in ordinary air cylinders is stiction, which is the tendency for a cylinder to stick in the initiation of movement, or during continuous movement. To overcome this, Anti- Stiction ® technology provides an ultra-low friction air cylinder called Airpel.
Airpel is constructed with a graphite piston, custom fitted inside a precision Pyrex® glass cylinder. The fit is designed to produce a small 0.0005-in. gap between the piston and the glass cylinder so that when pressurized, the piston is surrounded by a cushion of air. The result is an ultra-low friction device with virtually no starting friction or running friction. By eliminating stiction, Airpel allows a high degree of control over the force that the air cylinder can apply. This is exactly what was needed for the control of the dancer am.
Airpot Corporation manufactures instrument quality, precision Air Dashpots, Snubbers, Pneumatic Actuators, Airpel Anti-Stiction Air Cylinders and -AB Air Bearing Actuators. Airpot welcomes custom requirements and works with customers to adapt products to suit their individual application needs. Value added sub-assembly services are also a specialty. Airpot Corporation is a trusted supplier to many of the world’s most prestigious original equipment manufacturers. Visit www.airpot.com for detailed specifications. Call or email our technical staff for application assistance and ordering information. service@airpot.com 203-846-2021.
Key Markets: Semiconductor, Electronics, Medical Devices, Metrology, Test & Measurement, Laboratory Diagnostics.
Key Applications: Filament & Wire Tensioning, Positioning and Manipulating Optics, Liquids, Delicate Devices, Super Sensitive Force Control, Counterbalancing and Safety For Vertically Positioned Linear Driven Motor Masses, Measuring Weight, Creep, Tensile Strength and Calibration
Marketing Contact: Edward Keane edkeane@airpot.com
Technical Contact: Tom Lee tlee@airpot.com
203 846 2021 www.airpot.com
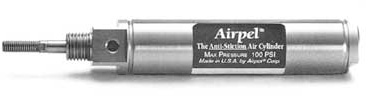
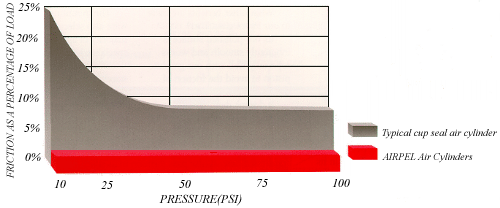